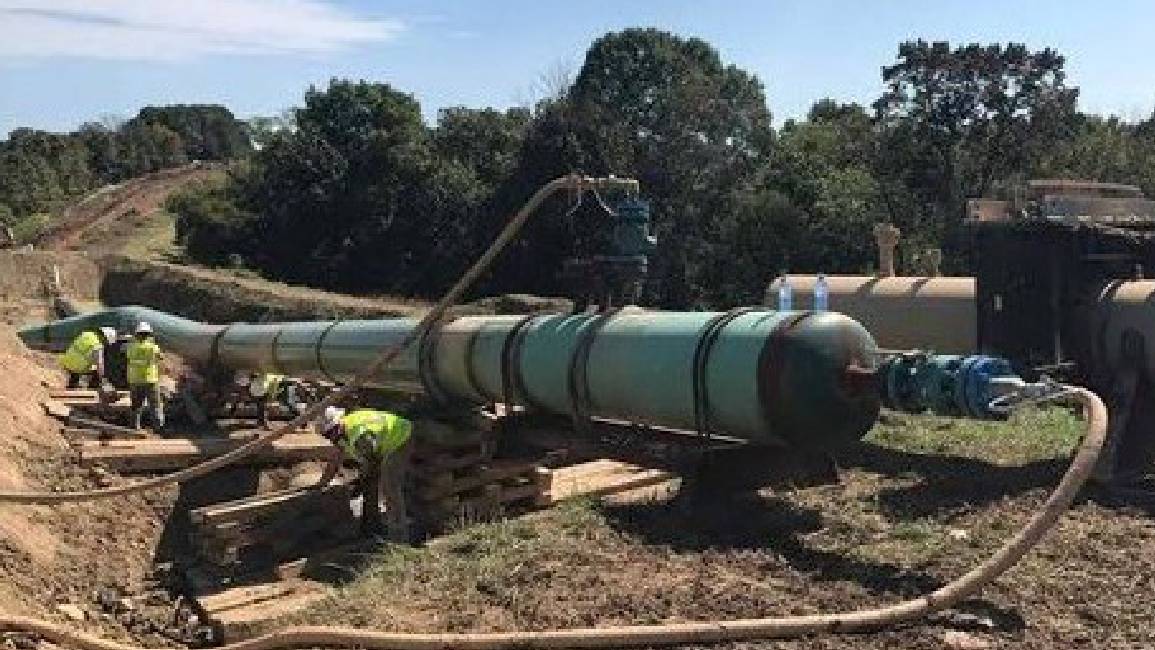
Services
Hydro Testing, Pressure Testing Inspection and Certification
PGSL offers pressure testing of pipelines, Vessels, Elbows, Hoses, Cargo Hoses, Pipelines, Pipe spools, Control Valves, Actuators, Oil Suction Hoses, Water Hoses, Skids, Pressure Vessel, Manifolds, Air compressors, etc.,
Pipe spools and chambers either by using water(Hydro Testing) or by Air(Pneumatic Test).A Pressure test conducted to prove the integrity of pressure vessel with the use of liquid medium is known as Hydro test or hydrostatic test. The fluid used in the flushing or hydrostatic testing operation which is normally clean / fresh water or treated fluid. (Where applicable a suitable corrosion inhibitor, chloride controlled water, combination or mixture of such are used to prevent the possibility of damage due to the adverse effect of water on the pressure vessel material of its product service). Pressure Test carried out to prove the integrity of pressure vessel, nozzle, Chamber, reinforcement pads etc. with the use of dry compressed air or inert gas and water / soap solution is called Pneumatic Test.
A Pressure test conducted to prove the integrity of pressure vessel with the use of liquid medium is known as Hydro test or hydrostatic test. Prior to the Hydrostatic test or hydro test, inspector will ensure the installation of blind flanges/gaskets in nozzles and vents for air ventilation to avoid air pockets. Keeping the vents always open during the filling process. Hydro test medium shall be clean fresh water or for the hydro testing of Stainless steel materials, clean fresh water or less chlorinated water shall be used for the hydro testing in order to avoid corrosion. Test pressure of Hydro testing services shall be 1.5 times of design pressure and/or the factors by considering the design and test temperatures. Two Pressure gauges along with chart recorders are used to record /indicate the pressure ranges. Ideally hydro testing pressure gauges will be located at the top of the vessel with an independent nozzle separate from the hydrotest pump. Safety Checks of Hydrotest includes ensure proper gaskets/nuts &stud bolts, barricade area etc. PGSL always uses calibrated pressure gauges and chart recorder with Temperature/Pressure test recorders as per the ASME/API Code requirements.
Hydro test Safety Rules & Guidelines:
- Isolate the hydro test areas with tiger tape and attach the warning signs.
- Never hydro test against a closed valve that is the parts of the system.
- Ensure Proper gasket, Blinds with pressure ratings, Nut &Stud bolts prior to hydro testing.
- Always wear Proper PPE within hydro testing areas/ boundary.
- Maintain a min. distance of 3m between vessel/miscellaneous fittings(flanges/coupling) and hydro test personnel during build of hydro test pressure.
- While hydro testing of large vessels, consider a suitable wetting agent to reduce surface tension and it reduces air pockets.
- Build hydro test pressure gradually in steps, providing sufficient time for all piping to equalize strains during hydro testing.
Pipe freezing is a method of liquid nitrogen applied in the outer surface of pipes to lower the temperature of pipes .When the temperature of pipes lower than the pipe fluid below its freezing point, create a freeze plug capable to withholding pressure up to 4000psi.Pipeline freezing is used for valve/pump replacement, pressure testing and HVAC System maintenance etc.Pipe freezing is ideal for pipes varies from ½’to 30 “.Pipe freezing services are used for Refineries, Petrochemical plants, Transmission pipeline, Power Generation, Fire Protection system, office Buildings, Hospitals ,Schools etc. Typical pipe freezing holding time are for ½’pipe freezing ,it is 6 minutes; Pipe freezing for 6” pipes, it is 48 minutes, pipe freezing holding time for 8”pipe is 90 minutes, Pipe freezing time for 12’”pipe is 3 hours, Pipe freezing holding time for 20”pipe is 4 hours etc. Fluid Capabilities in pipe freezing services are water, sewage, oil, glycol, brine etc. Benefits of pipe freezing services are eliminates needs for bulk fluid transfer or storage, eliminates need for draining down system, and venting procedures, enhances safety while working on lines containing hazardous liquids.
Boilers and pressure vessels are used all over the world in different industries including oil and gas and energy industries. In order to ensure safety and operational efficiency of pressure vessel equipment, certain regulations and codes have been developed, some of which require independent inspection and certification to achieve compliance. PGSL provides pressure vessel and piping inspection surveys to ensure that statutory inspections and remaining life assessments are conducted, and equipment continues to remain safe to use.
Our Capabilities :
- Engineering Evaluations
- Mechanical Integrity
- Thickness Inspections
- Fitness for Service Evaluations (FFS)
- Corrosion Rate and Remaining Life Determination.
- Turnkey Management Program.
- Jurisdictional State Special Evaluations.
Pressure Vessels within our expertise include:
- ASME Section VIII, Division 1.
- ASME Section VIII, Division 2.
- (PED) 2014/68/EU.
- Deaerator Tanks.
- Heat Exchangers.
- Glass Lined Vessels.
- Autoclaves.
- Research Vessels.
- Dryer Cans and Yankee Dryers.
It is important to the success of your company are the assets you rely on each day. These include your plant processes and equipment. Keeping them safe and reliable is your goal. Our pipe line integrity management and piping Inspection include pipe line feasibility study, pipe line inspection procedure and budget developments, reporting and recommendations etc. EIWAA offers comprehensive package of consultancy and project support services with the capability of performing industry focused research and development contracts. Our experts having skills and experience in materials and material science, electro chemistry, corrosion and life assessment.
In many situations, it is not possible to find out the surface area of a given assets, such as a pipeline or a heat exchanger. Where the mode of damage is pitting corrosion, we provide a range of services to obtain required information for confident life assessment.
Using extreme value statistical methods, EIWAA’s API Inspection Engineers calculate the expected depth of the deepest pit based on inspection results from only a small fraction of the surface area. The extent of inspection required depends on the severity and quantity of the pitting damage. In cases where there is excessive or little to no pitting, inspecting 10% of the total area is often sufficient. In cases that are indistinct, we use sequential decision theory to implement inspection test plans based on the degree of risk associated with each case.
Our Capabilities :
- Engineering Evaluations: Pressure and Structural Calculations.
- Fitness for Service Evaluations (FFS).
- Risk Based Inspections (RBI).
- Damage Mechanism Driven Inspections.
- Corrosion Rate and Remaining Life Determination.